加載中![]()
一、發(fā)電機(jī)轉(zhuǎn)子技術(shù)參數(shù)
1、#5機(jī)發(fā)電機(jī)轉(zhuǎn)子汽端軸頸及密封瓦軸頸
2、發(fā)電機(jī)、汽輪機(jī)型號:QFSN2-330-2、N330-16.7/538/538
3、軸頸尺寸:Ф450
4、生產(chǎn)廠家:上海電氣
5、發(fā)電機(jī)轉(zhuǎn)子軸頸材質(zhì):25Cr2Ni4MoV,軸頸直徑:Ф450h7
6、修復(fù)內(nèi)容:#5發(fā)電機(jī)轉(zhuǎn)子汽端軸頸及密封瓦軸頸,長度約450mm+45mm,深度約0.3~2.5mm 。
▲修復(fù)前
二、修復(fù)工藝流程(激光增材再制造)
1、施工前準(zhǔn)備:
1.1、根據(jù)轉(zhuǎn)子材質(zhì)和工況條件選擇專門使用的激光熔覆粉末,其熔覆粉末性能滿足轉(zhuǎn)子運(yùn)行工況條件。
1.2、根據(jù)轉(zhuǎn)子重量及機(jī)械尺寸調(diào)整改進(jìn)轉(zhuǎn)子機(jī)加工的旋轉(zhuǎn)工裝及附件。
1.3、根據(jù)出現(xiàn)場設(shè)備與修復(fù)工作準(zhǔn)備所用工器具及相關(guān)物資。
1.4、做好出現(xiàn)場人員準(zhǔn)備工作。
1.5、確定修復(fù)日期后,激光設(shè)備拆卸、相關(guān)設(shè)備工器具物資裝車、發(fā)運(yùn)往修復(fù)現(xiàn)場。
2、現(xiàn)場設(shè)備安裝和調(diào)試
2.1、設(shè)備運(yùn)抵現(xiàn)場后,根據(jù)現(xiàn)場空間位置進(jìn)行合理空間布局,并對設(shè)備進(jìn)行逐一調(diào)試,使設(shè)備均處于良好的工作狀態(tài)。
2.2、現(xiàn)場作業(yè)的具體要求:
2.2.1、激光熔覆用粉末現(xiàn)場進(jìn)行烘干處理。
2.2.2、作業(yè)前保證高純氦氣能夠滿足生產(chǎn)需要。
2.2.3、作業(yè)過程中不定期對保護(hù)鏡片進(jìn)行檢測,發(fā)現(xiàn)損壞及時(shí)更換。
2.2.4、熔覆過程中每4小時(shí)對設(shè)備進(jìn)行巡檢,檢查內(nèi)容填入《設(shè)備運(yùn)行記錄表》,發(fā)現(xiàn)問題及時(shí)調(diào)整和維護(hù),工作過程中還要不定期進(jìn)行檢查。
2.3、激光設(shè)備安裝調(diào)試:
2.3.1、激光器、機(jī)器人、加工設(shè)備安裝和調(diào)整。
2.3.2、激光器設(shè)備動力電源的安裝。
2.3.3、激光器的調(diào)試。
2.3.4、機(jī)器人調(diào)試。
2.4、按照已確定的軸頸激光熔覆工藝參數(shù),現(xiàn)場熔覆試塊制作(因設(shè)備經(jīng)過拆機(jī)、運(yùn)輸、重新安裝,通過試塊制作質(zhì)量的觀察檢驗(yàn),確保機(jī)器人、激光器等設(shè)備運(yùn)行狀況良好穩(wěn)定)。
3、現(xiàn)場測量及探傷
3.1、對確認(rèn)后的損傷部位的尺寸檢測,無損檢測(著色探傷)。
3.1.1、選用千分尺對該軸頸段進(jìn)行尺寸檢測。檢測時(shí)尺寸頸向與軸向多點(diǎn)檢測,能客觀反映出原始軸段的橢圓度和錐度。
3.1.2、選用著色探傷對該軸頸段(軸頸先清理)進(jìn)行無損檢測,檢測結(jié)果作為原始記錄。
3.1.3、無損探傷檢測表面是否存在微裂紋。
3.1.4、檢測表面硬度。
3.1.5、初步檢測確認(rèn)進(jìn)行激光熔覆各部位的形位公差。
3.1.6、定量確認(rèn)后期加工內(nèi)容和尺寸(雙方現(xiàn)場確認(rèn))。
4、損傷部位疲勞層清理
4.1、利用隨形機(jī)加設(shè)備對損傷部位進(jìn)行機(jī)械清理。遵循***小去除量原則,極大程度不損傷完好的基材部位。
4.2、車削損傷部位,要注意損傷部位兩端與未損軸頸交接處,需要斜角(60度)過渡,底部槽與斜面要形成r角(大于R5)過渡,以便激光熔覆和消除軸頸原始損傷部位應(yīng)力集中問題。
4.3、損傷部位初加工后,經(jīng)著色檢測確認(rèn)無潛在缺陷方可,并檢測記錄損傷部位加工后尺寸(修復(fù)部位直徑(位置)*長度*深度)。
4.4、清理前,須做周邊部份防護(hù)工作,確保防護(hù)嚴(yán)密。
5、激光熔覆加工
5.1、對去除疲勞層后的修復(fù)部位進(jìn)行徹底清理,采用化學(xué)品除油,并用清洗溶劑清洗,確定無任何油漬與殘留物方可。
5.2、根據(jù)軸頸的具體實(shí)際尺寸進(jìn)行機(jī)器人編程,并校驗(yàn)程序的可靠性,采用同步送粉的方法對軸頸熔覆。
5.3、對需要加工軸頸部位按照已確定的軸頸激光熔覆工藝參數(shù)進(jìn)行激光熔覆(軸頸表面分段熔覆,轉(zhuǎn)子每隔圓周方向30度左右進(jìn)行盤車旋轉(zhuǎn),需要甲方配合盤車)。
5.4、結(jié)尾的一層激光熔覆厚度,高于基體面約0.5mm,確保加工余量。
5.5、熔覆結(jié)束后對表面的高點(diǎn)進(jìn)行打磨處理,以便于精修加工。
5.6、熔覆尺寸(直徑(位置)*長度)、硬度、探傷檢測。拍照并存檔。
6、軸頸的機(jī)加復(fù)形
6.1隨形機(jī)加設(shè)備輔助裝置的安裝。
6.2設(shè)備調(diào)試。
6.3加工部位的外形尺寸檢測。
6.4機(jī)加工藝參數(shù)的確定。
6.5隨形切削機(jī)加工。
6.6機(jī)加工后的尺寸精度檢測(雙方書面簽字確定)。
6.7機(jī)加工后的無損探傷檢測(著色探傷、超聲波探傷)
▲修復(fù)時(shí)
三、質(zhì)量保證
1、激光熔覆位置不發(fā)脫落,起皮等焊接缺陷。
2、確保發(fā)電機(jī)軸頸修復(fù)部位不脫落,無氣孔、無裂紋、無雜質(zhì)等缺陷。
3、確保激光增材再制造過程及修復(fù)部位不發(fā)生電化學(xué)腐蝕及其它對轉(zhuǎn)子軸頸的損傷。
4、軸頸修復(fù)修復(fù)后軸頸橢圓度≤0.02mm;修復(fù)后軸錐度≤0.02mm;修復(fù)后同心度≤0.02mm。
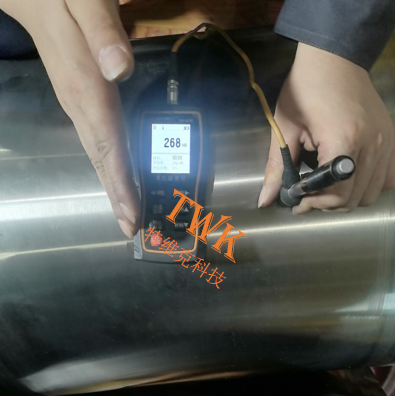
▲修復(fù)后
加載中